Barry on Batteries: The Battery Material Nobody Talks About
What You’ll Learn
- Graphite is a critical but often overlooked component of lithium-ion batteries, making up to 28% of a battery by weight and being the largest component by volume.
- Recycling recovers graphite from battery black mass, including air jet sieving, selective flotation, and processes using green solvents or heat treatment to enhance recovery efficiency.
- Graphite must undergo significant processing for use in lithium-ion batteries. This includes "grinding and rounding" the graphite, then mixing with wetting agents and binders to form an anode slurry that coats copper foils in the battery manufacturing process.
Lithium-ion batteries contain multiple critical materials—lithium, nickel, cobalt, manganese and graphite — along with plastics and chemicals like electrolytes and binders. While lithium ions generate the power and other metals provide protection and capacity, graphite in the anodes stores the lithium ions. Yet when supply chain discussions focus on lithium, graphite remains the forgotten child.
This oversight is significant. Graphite can comprise up to 28% of a battery by weight and represents the largest component by volume. A single lithium-ion battery requires approximately 10-15 times more graphite than lithium. During recycling, after mechanical shredding and granulating, graphite can make up 40% of the resulting black mass.
Understanding graphite's role — from sourcing and processing to recycling — reveals why this material deserves equal attention in the circular economy of battery materials.
But first, a little background on graphite. Natural graphite is mined from the earth’s surface in two forms. They include medium and fine flake graphite, which comes from metamorphic rock, and amorphous graphite extracted from coal seams.
A third very rare form is vein graphite, primarily sourced from Sri Lanka. Nearly 95% of battery-grade natural graphite comes from China, with Japan and the United States supplying the remaining 5%. Madagascar, Mozambique and India produce non-battery grade graphite.
The limitations of the natural supply chain has led to the development of synthetic graphite. Synthetic graphite is produced from petroleum, or needle, coke in high-temperature furnaces. The process is energy intensive and generates a significant amount of greenhouse gas emissions. The introduction of more energy-efficient furnaces as well as current research into renewable energy sources, such as wood biomass, could minimize these impacts.
To make this graphite usable in LIBs, it must be processed using methods that produce a final product with a 99.95 % or higher purity level. Shape and size also play an important role. For example, spherical graphite (SPG) is required for the anodes. SPG with smooth and small surfaces results in low-capacity loss and long service life.
Grinding and rounding technologies are now available to produce rounded graphite at various particle size distributions to meet different production requirements. Battery producers form the anode slurry by mixing the graphite with wetting-agents and binders and then coating copper foils with this slurry before final drying and cell manufacturing.
Recycled Graphite
Recent research has demonstrated that recycled graphite can match the performance of natural and synthetic graphite in LIBs. At the International Battery Seminar, where I served as both presenter and session chair for the recycling session, Orbia Fluor and Energy Materials (Orbia F&EM) presented data on this topic. Their findings show that recycled graphite anode active material delivers identical performance to fresh graphite in terms of physical properties (particle size distribution, surface area, purity and tap density) and operational cell characteristics (capacity retention and capacity performance).
The recycling process begins with mechanical pretreatment, including shredding and granulating, of LIBs to produce black mass and mixed materials. Vacuum drying removes and recovers the electrolyte. Battery recyclers then sort and classify the material by size and density. A percentage of the graphite remains with the black mass and a percentage remains with the mixed material. The percentages depend upon the recycling process.
The tricky step is then to recover the graphite from the black mass and the mixed material, which occurs downstream at the hydromet or mixed-material facility. Graphite is very chemically stable, has a small particle size distribution and is coated with the battery binder. These three parameters cause headaches for the downstream processes especially as the binders must be removed/dissolved before attempting to remove the graphite.
One of the recovery methods currently in the research phase involves air jet sieving by density and size. This process can recover graphite from the aluminum and copper foils after heat treatment or solvent dissolution of the binders.
Selective flotation of the black mass or mixed materials is another promising technique. Flotation by density of the material and using different solvents has resulted in improved recovery. Green solvents are also being developed for sustainable graphite recovery. To enhance the recovery efficiency, the different materials can be roasted between 350 and 450°C and then subjected to flotation.
Graphite recovery and recycling are just beginning to be recognized as equally important to metals recovery. As global battery production scales rapidly, it could prove to be just as critical to building a truly circular battery economy.
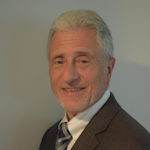
Barry Perlmutter | President of Perlmutter & Idea Development (P&ID) LLC
Barry Perlmutter is president of Perlmutter & Idea Development (P&ID) LLC. He has over 40 years of science, engineering and business marketing experience in the field of solid-liquid separation including filtration, centrifugation, process drying, mixing and recycling. His strong professional skills focus on process and project solutions, innovation strategies and execution, market expansion and business development. Barry has published and presented worldwide on applications in the chemical, pharmaceutical, and energy/environmental industries and has been responsible for introducing many European technologies into the Americas marketplace. His two books, published by Elsevier, Amsterdam, "Handbook of Solid-Liquid Filtration" and "Integration & Optimization of Unit Operations" are used worldwide for process guidance.