Barry on Batteries: Engineering Safety Into Lithium-Ion Recycling
Key Takeaways
- Recycling lithium-ion batteries requires chemical industry-level safety protocols — like HAZOPs (hazard and operability studies) and PHAs (process hazard analyses) — to prevent accidents and ensure process safety.
- Dust (e.g. generated at shredding, drying and sorting stages) and electrolyte handling are major safety challenges. The dust can be combustible; electrolytes are often flammable and toxic. Both require controlled handling, vapor recovery systems, and gas-tight equipment to meet OSHA and environmental regulations.
- Involving experienced chemical engineers and adopting a holistic safety culture are essential for successful, incident-free battery recycling operations.
Lithium-ion batteries (LIB) contain metals, plastics and chemicals that processors must handle safely during the recycling process.
Many hazards exist when processing these materials, including exposure to combustible dust and flammable, corrosive and toxic electrolytes.
To ensure a safe environment, operators should begin with hazard and operability studies (HAZOPs) to check designs for safety risks. The HAZOPs should involve many disciplines from the plant, such as operators and process engineers, to ensure all safety aspects are fully explored. In addition, it’s important to conduct process hazard analysis (PHA) reviews during preliminary engineering of the recycling process to ensure that safety can be designed into it.
In the recycling process, typically there may be up to 25 unit operations with over 100 individual process lines or equipment to evaluate.
Managing Combustible Dust: A Multi-Stage Challenge
Dust is generated at multiple stages throughout the battery recycling process. During the mechanical pretreatment stage, the shredding and granulation of either metal or plastic creates dust. This dust poses a fire hazard, especially when working with lithium batteries, as dust particles are highly combustible in the presence of oxygen. By conducting these processes in an inert nitrogen environment, the risk of ignition is eliminated since combustion cannot occur without oxygen.
Of course, if this is a wet shredding and granulating process, there is no dust but rather wastewater to handle. In the process vacuum drying stage, dust forms during electrolyte evaporation.
The sorting and classification phase produces additional dust as materials are separated. When separating the black mass — containing lithium, cobalt, manganese and nickel — from other components like plastics, copper and aluminum, processes such as sieving, milling and density separation all contribute to dust formation. Finally, both the packaging and conveying of these recovered powders serve as additional sources of dust generation.
Chemical engineers who are familiar with dust handling know the inherent dangers, including the potential for explosions. To mitigate these risks effectively, data gathering becomes a critical step in designing safe recycling processes.
Independent labs can conduct combustible dust analyses using various American Society for Testing and Materials (ASTM) methods according to ASTM E1226. In addition, the labs will perform sample characterization testing to determine the sample’s moisture content, particle size distribution and shape.
Once this testing is completed, engineers should also reference the National Fire Protection Association (NFPA) 660 standards for combustible dusts and particulate solids. This information helps engineers design the process for dust containment, which includes the use of dust filters (cartridges and pulse-bag units), dust-tight conveyors and dust piping. The dust piping allows for a complete dedusting system, which is typically outside of the process building, and dust handling within the building and the HVAC systems.
Electrolyte Containment and Recovery
The electrolyte is the liquid part of the battery, and the first step in this recycling process is to determine the electrolyte composition. For each battery manufacturer, this is the “secret sauce” for the battery, so it may be difficult to obtain. Whenever possible, plants should sort the different batteries they receive to categorize the composition types.
Electrolytes contain many components, so safety data sheets are required. They are typically flammable, toxic and corrosive. Another safety consideration that requires further investigation is the possibility of byproducts generated during the recycling process, such as hydrofluoric acid. This must also be included in any process design and any cleaning solvents being used.
The wet-shredded battery materials are conveyed to the process vacuum dryer. While the dust conveyors are dust-tight, the conveyors for this part of the process must also be gas-tight, which is an interesting challenge for suppliers.
The electrolytes are evaporated during the process vacuum drying step and then must be treated to be recovered in the process design to meet U.S. Occupational Safety and Health Administration and NFPA standards, as well as the local environmental emission regulations for volatile organic compounds (VOCs).
Depending on the process, some plants may use condensers at different temperatures for initial recovery and final recovery. Process plants can treat the acid gases with scrubbers and specific scrubbing liquids for neutralization. Thermal oxidizers can also be installed for VOC control.
Many other safety issues are addressed during the HAZOP and PHA studies. For example, engineers will consider the National Electrical Code requirements for instruments, wiring and controls. The correct personal protective equipment must also be included in the safety design reviews.
Other considerations include battery receiving, storage, electrical discharging for dry recycling, shipping of the final separated products and safety equipment, such as fire suppression, blowout protections, early detection monitoring, instrumentation and automated controls.
Also consider guidelines for labeling, signs, training and administrative controls. LIB processing safety involves certain aspects that are common in the chemical industry. Safety starts with leadership and employee involvement. As these facilities are new in terms of operation, chemical engineers can bring a wealth of knowledge and experience to these processes.
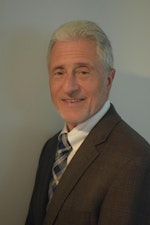
Barry Perlmutter | President of Perlmutter & Idea Development (P&ID) LLC
Barry Perlmutter is president of Perlmutter & Idea Development (P&ID) LLC. He has over 40 years of science, engineering and business marketing experience in the field of solid-liquid separation including filtration, centrifugation, process drying, mixing and recycling. His strong professional skills focus on process and project solutions, innovation strategies and execution, market expansion and business development. Barry has published and presented worldwide on applications in the chemical, pharmaceutical, and energy/environmental industries and has been responsible for introducing many European technologies into the Americas marketplace. His two books, published by Elsevier, Amsterdam, "Handbook of Solid-Liquid Filtration" and "Integration & Optimization of Unit Operations" are used worldwide for process guidance.