Energy Saver: Process Intensification Maximizes Output, Minimizes Resources
What You'll Learn
- How process intensification technologies like reactive distillation and membrane reactors reduce energy consumption by 20%–60% and capital costs by 10%–30%.
- Why rethinking entire unit operations — not just optimizing them — creates new opportunities for efficiency, throughput and sustainability.
- What practical strategies manufacturers can use to overcome scale-up, cost and workforce barriers when implementing PI in existing plants.
Eleven steps into one. That’s how one chemical company transformed their production of methyl acetate by collapsing a sprawling process into a single, intensified unit. One reactive distillation column. That’s it. Along the way, the company significantly reduced energy use, capital costs and complexity in one stroke (Cogswell, 2024).
This is the essence of process intensification (PI), a powerful and elegant route to deliver more with less, delivering energy savings of 20%-60% while simultaneously reducing capital costs by 10%-30% across diverse applications (Li et al., 2024).
With just 11 chemicals, the U.S. Department of Energy (DOE) estimates over $9 billion in annual cost savings with PI. That's not a typo; it’s the opportunity awaiting manufacturers who embrace PI to gain a competitive advantage (U.S. Department of Energy, 2015).
Over 150 commercial installations are known to implement PI to success. Meanwhile, competitors using conventional systems face higher energy costs and reduced competitiveness. To oversimplify, the everyday person would see it like one company carrying a beeper, basic phone and personal digital assistant (PDA… remember those?) and another company carrying a modern smart phone to operate in the modern business environment. Which company are you positioning to be?
Rethinking Unit Processes
Here's what PI really means: reimagination, not incremental tweaking. Traditional approaches optimize individual unit operations, whereas PI changes the boundaries between them, creating compact, multifunctional devices that build upon fundamentals to create new paradigms of operational and energy efficiency (Keil, 2018).
Furthermore, DOE didn't pull that $9 billion figure from thin air. The agency’s analysis identified 695 TBtu/year of potential energy savings using proven technologies, not laboratory or early-stage technology. We're talking about real equipment in real plants generating real profits (see Table 1: Examples of process intensification).
Take reactive distillation, perhaps the poster child of PI success. These are the known 150-plus installations globally that routinely reduce energy consumption by 20%-60% while improving product quality. By combining reaction and separation into a single vessel, they eliminate intermediate storage, reduce equipment counts by half, and turn thermodynamic limitations into advantages (Kiss & Smith, 2020).
Reactive distillation utilizes reaction heat for separation while continuously removing products, achieving thermodynamic synergies not possible with sequential processing. For example, reactive distillation for ester production saved energy and reduced CO₂ emissions in one facility by 61.8% while maintaining 99%-plus purity (Li et al., 2024).
In addition to reactive distillation, PI extends to miniaturized and selective separation technologies that push the boundaries of reaction efficiency even further.
Microreactors represent the extreme end of size reduction in process intensification. With channels measuring just 10-500 μm, they achieve truly impressive heat transfer coefficients up to 100 to 50,000 times conventional equipment (Roberge et al., 2005). Despite their microscopic dimensions, manufacturers now push 10,000-plus metric tons annually through these tiny systems, with individual units running 8,000 hours or more per year in challenging conditions (Jiang, 2022).
Membrane reactors take a different approach by selectively removing products as they form, overcoming thermodynamic limitations that constrain traditional reactors. For example, advanced palladium systems boost hydrogen production conversions by 30% (Khoiruddin et al., 2024).
The Intense Truth About Implementation
If PI were easy, everyone would already be doing it. The barriers are real but surmountable. Scale-up and integration is a concern given the nature of chemical plants. For example, going from eleven columns to one can leave a gaping hole where previous dependencies, such as heat transfer and intermediary feedstocks, are now missing.
Capital constraints can create another speed bump. Even if paybacks hit one to three years, the upfront check still needs signing. Smart operators have cracked this code through phased implementation. Consider starting with lower-risk technologies like dividing wall columns, bank those savings, then reinvest in other, potentially more advanced technologies (see Table 2: Basic checklist for process implementation).
Additionally, there's the human element. PI systems demand different thinking compared to traditional operations. Operators need new skills; engineers need new mental models. Progressive companies aren't waiting for academia to catch up; they're forging partnerships, building internal universities and creating the expertise they need.
Here's the uncomfortable truth: PI is evolving from competitive advantage to table stakes. Companies achieving 20%-60% energy savings aren't just improving margins. They are redefining what's possible in chemical manufacturing.
The convergence of digital technologies multiplies these advantages exponentially. AI-driven optimization, predictive analytics and real-time control are more accessible and commonplace. They're tools that transform static PI designs into living systems that continuously improve. Early adopters report 10%-15% additional gains beyond initial PI benefits. That's the difference between leading and following. [Note: see Energy Saver column ‘Digital Transformation: Unlocking Energy Efficiency in Chemical Processes’]
The $9 billion opportunity has an expiration date. Every day you delay, competitors gain ground. Markets shift. Technologies advance. Windows close.
Start with due diligence. Assess one process against PI suitability criteria. Partner with technology providers for pilot testing, then scale systematically based on your validated results and “intensify” from there.
References
Cogswell, C. (2024, May 13). Process intensification: The key to sustainability in chemical engineering. Elsevier Connect.
Gotama, B., Halomoan, T., Chen, Y. Y., & Lee, H. Y. (2024). Energy saving design and control of side-streams reactive distillation configuration for diphenyl carbonate production process. Chemical Engineering Research and Design, 204, 316-329.
Jiang, Y. (2022, October 9). Continuous flow reactors yield multiple benefits. Chemical Processing.
Khoiruddin, K., Kadja, G. T., Ismadji, S., & Wenten, I. G. (2024). Enhanced hydrogen production in membrane reactors: A novel approach. International Journal of Hydrogen Energy, 83, 946-966.
Keil, F. J. (2018). Process intensification. Reviews in Chemical Engineering, 34(2), 135-200.
Kiss, A. A., & Smith, R. (2020). Rethinking energy use in distillation processes for a more sustainable chemical industry. Energy, 203, 117788.
Li, Q., Somoza-Tornos, A., Grievink, J., & Kiss, A. A. (2024). Challenges and opportunities for process intensification in Europe from a process systems engineering perspective. Frontiers in Energy Research, 12, 1340635.
Roberge, D. M., Ducry, L., Bieler, N., Cretton, P., & Zimmermann, B. (2005). Microreactor technology: A revolution for the fine chemical and pharmaceutical industries? Chemical Engineering & Technology, 28(3), 318-323.
Tian, Y., Demirel, S. E., Hasan, M. F., & Pistikopoulos, E. N. (2018). An overview of process systems engineering approaches for process intensification: State of the art. Chemical Engineering and Processing–Process Intensification, 133, 160-210.
U.S. Department of Energy. (2015). Quadrennial technology review 2015: Chapter 6 - Process intensification. Advanced Manufacturing Office.
U.S. Department of Energy. (2022). The Rapid Advancement in Process Intensification Deployment (RAPID) Institute. Office of Energy Efficiency and Renewable Energy.
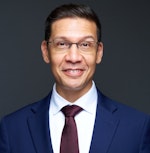
Thomas Kwan | Global Vice President, Strategic Innovation and Industrial Ecosystems
Thomas Alan Kwan is an energy transition expert at Schneider Electric's Sustainability Research Institute. With a Ph.D. in chemical and environmental engineering, he brings a blend of academic rigor and industrial experience to the field of sustainable manufacturing and green engineering.
At Schneider Electric, he leads initiatives focused on new and emerging industrial systems, with a particular emphasis on the chemical processing sector. His work involves developing innovative solutions and practices to drive energy, environmental and economic benefits.
Previously, he was a key member of Unilever's product engineering team, where he integrated green chemistry and engineering principles for product and process development. His contributions earned him a lifetime honorary membership on the team. Kwan also has experience in environmental regulation, having worked with the U.S. EPA on Clean Water Act programs.
Through his research and collaborations, Kwan continues to explore innovative ways to reduce energy consumption, minimize waste, maximize value and improve overall process efficiency in chemical manufacturing operations.